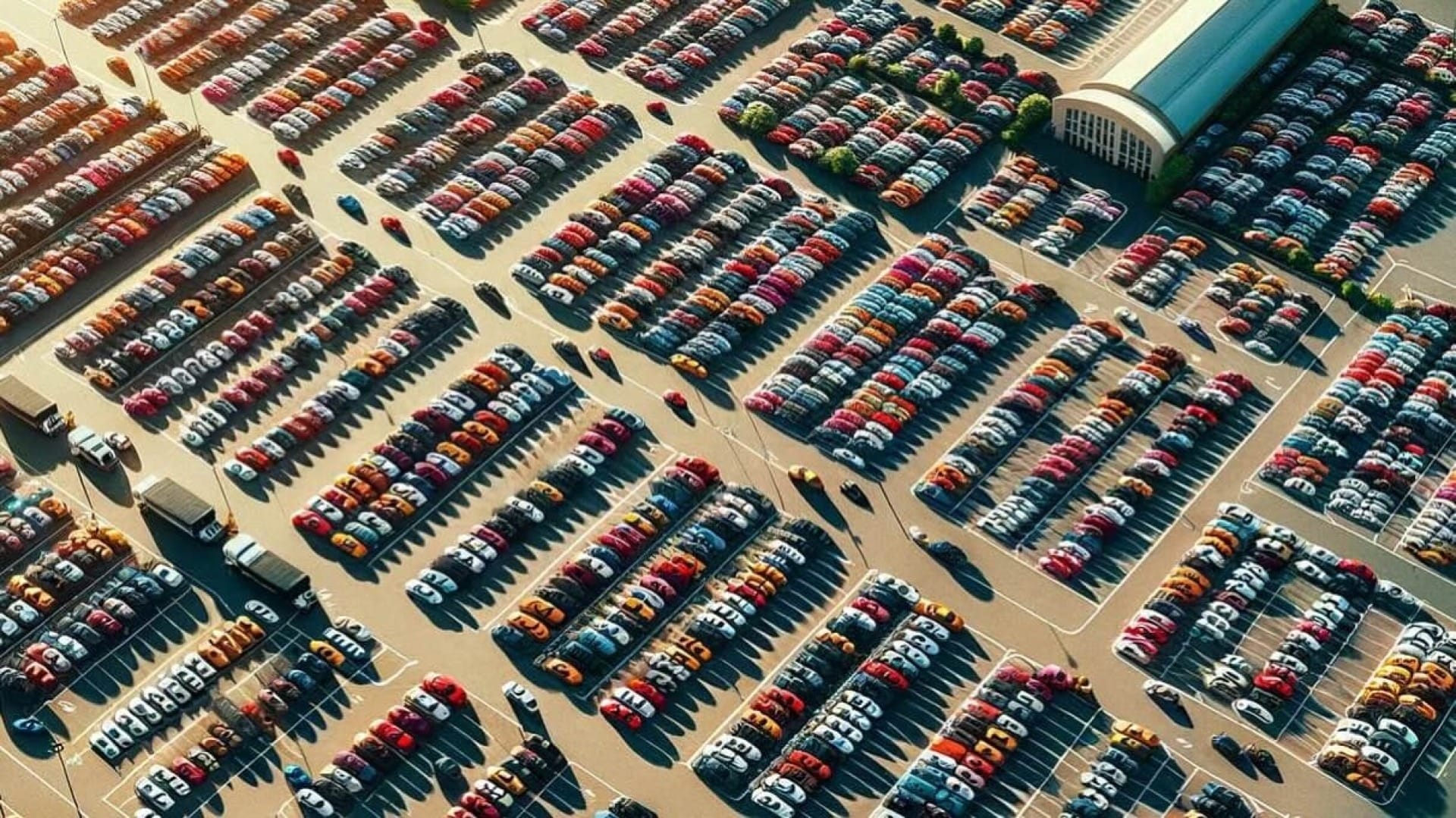
Automated Valet Parking: Roadside Autonomous Driving Explained
What it is and how it works, Roadside Autonomous Driving (RAD) solutions, a specific segment of the broader Automated Valet Parking (AVP) market.
The Roadside Autonomous Driving (RAD), also known as Automated Vehicle Marshalling (AVM), is a crucial segment of the broader Automated Valet Parking (AVP) market, which is witnessing a remarkable acceleration thanks to the integration of LiDAR technology.
The expected AVP market's growth trajectory from 2023 to 2031 is nothing short of impressive.
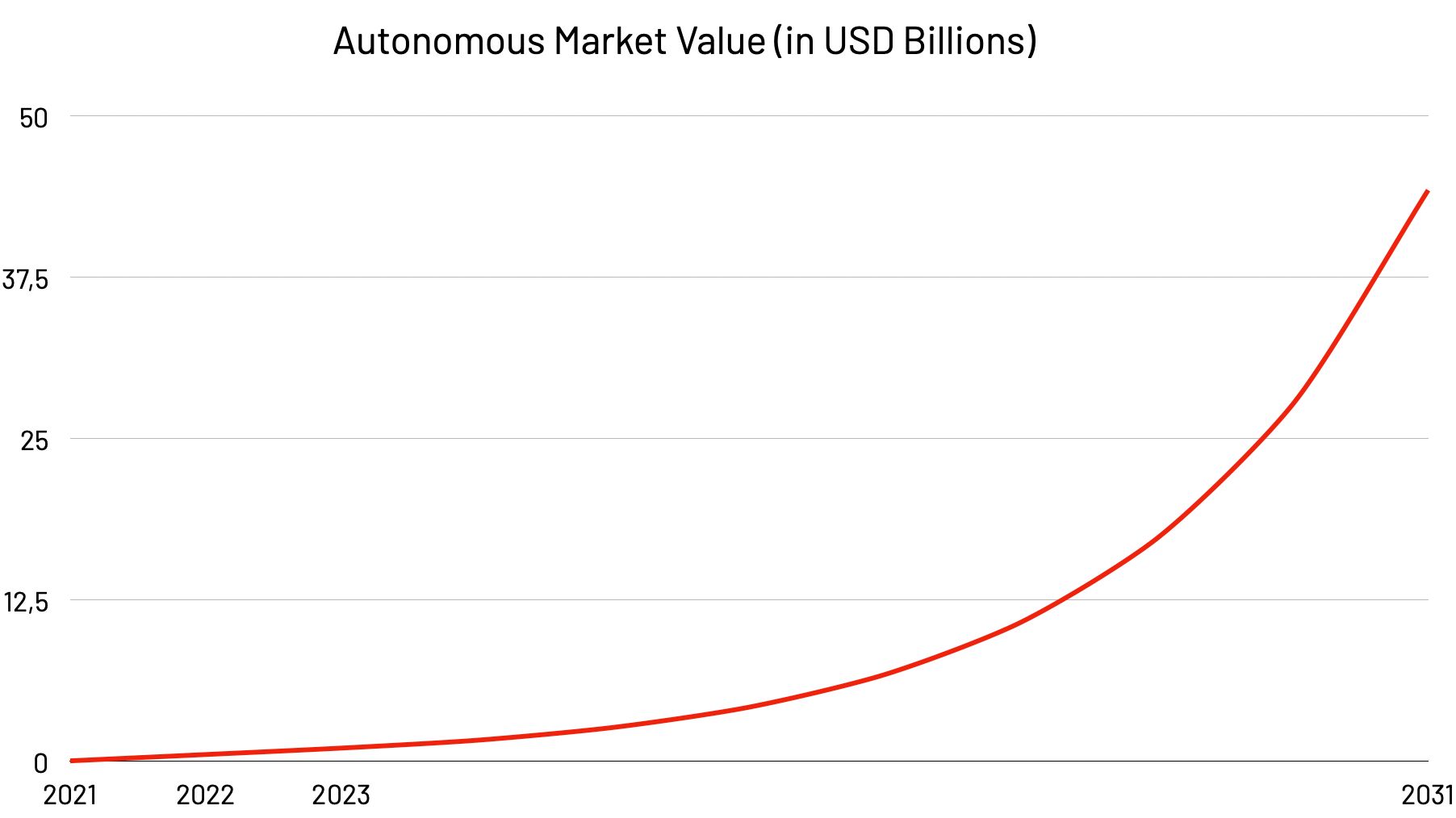
Starting at a value of approximately USD 1.02 billion in 2023, the market is projected to expand exponentially, reaching around USD 44.25 billion by 2031. This growth showcases the robust demand and potential for RAD and AVP solutions in the industrial domain.
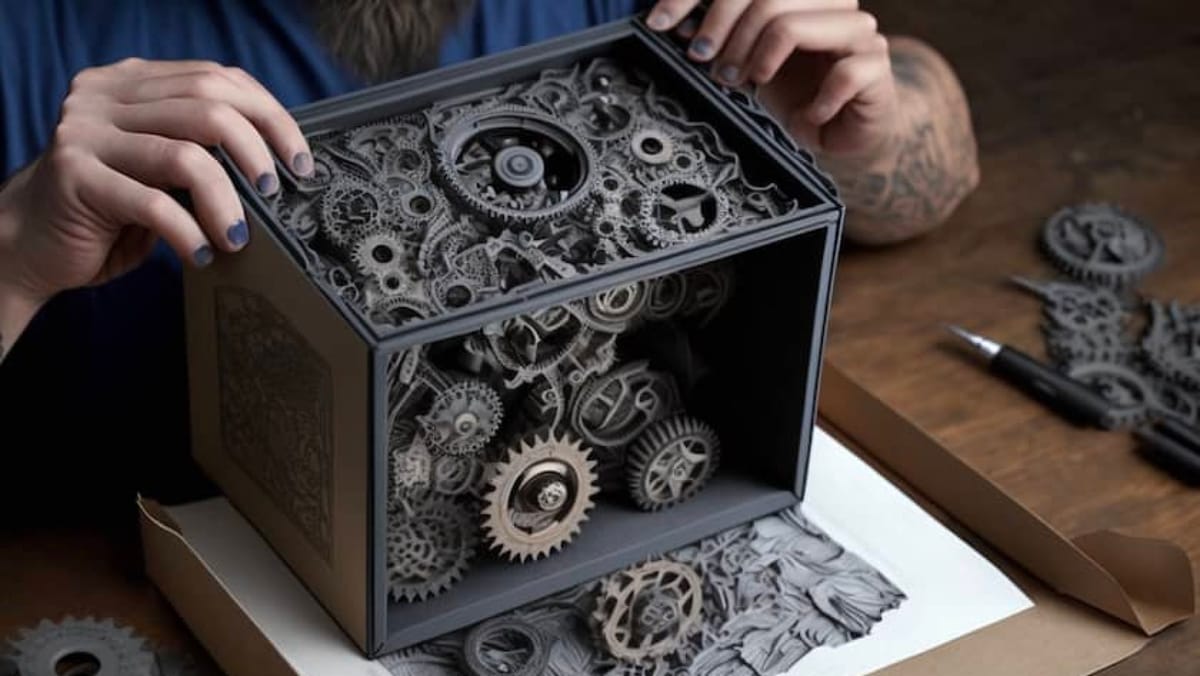
LiDAR's ability to accurately measure distances using laser light pulses makes it superior in many use cases, compared to other technologies like radar and cameras.
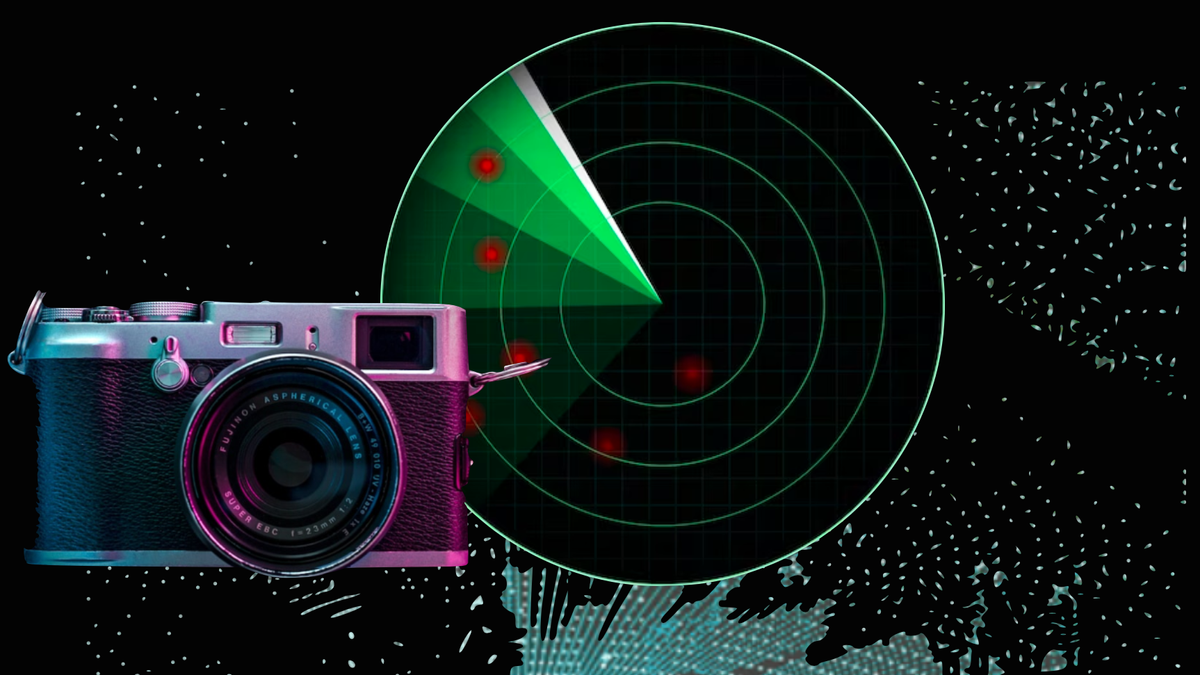
Manually Moving Vehicles in Factories is Inefficient
Traditional manual vehicle movement from production facilities are costly, as they involve drivers that manually take care of the task over long distances.
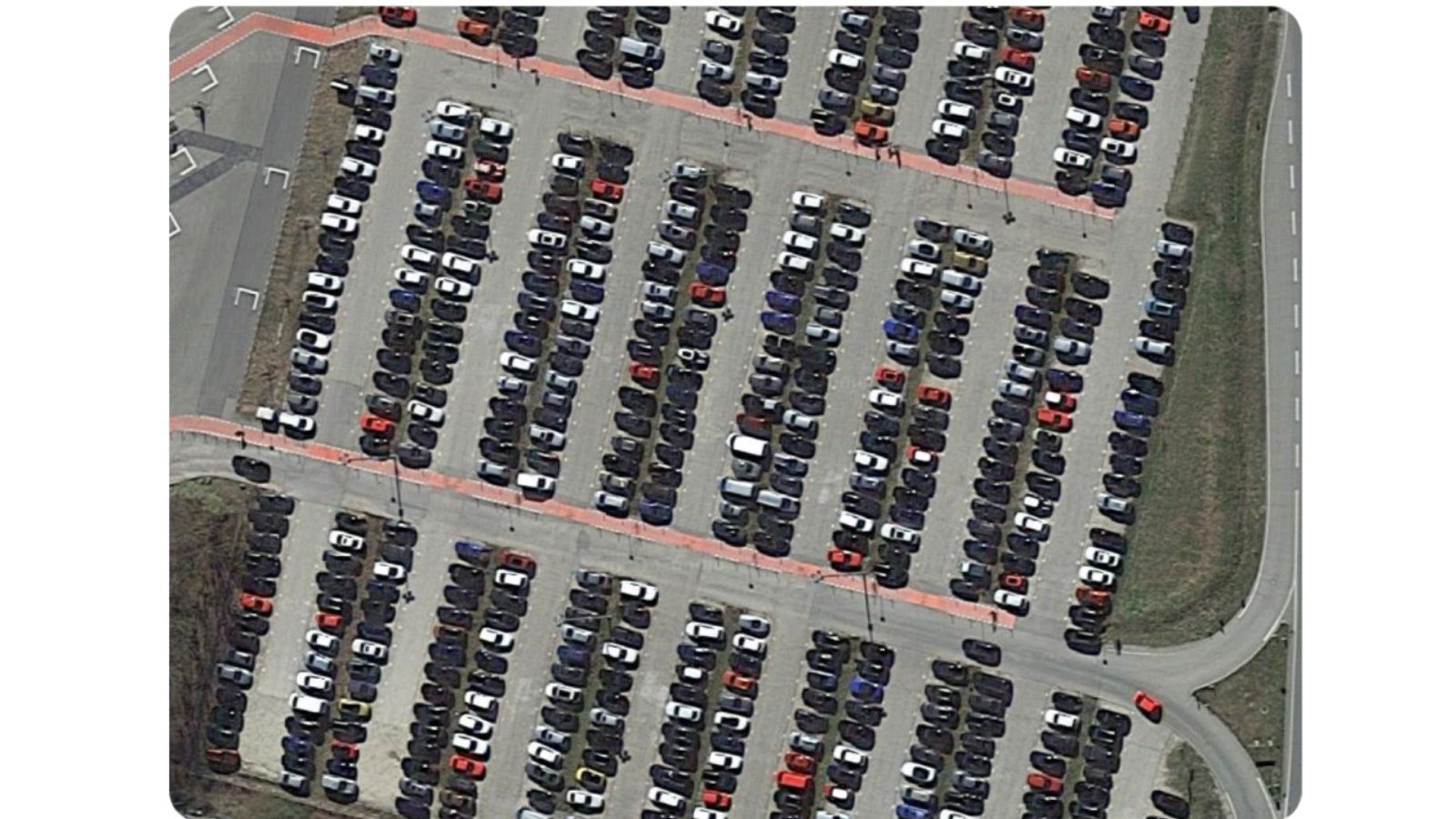
Until now, it was the only viable and reliable solution, but three new technology advancements are key enablers of a a new concept.
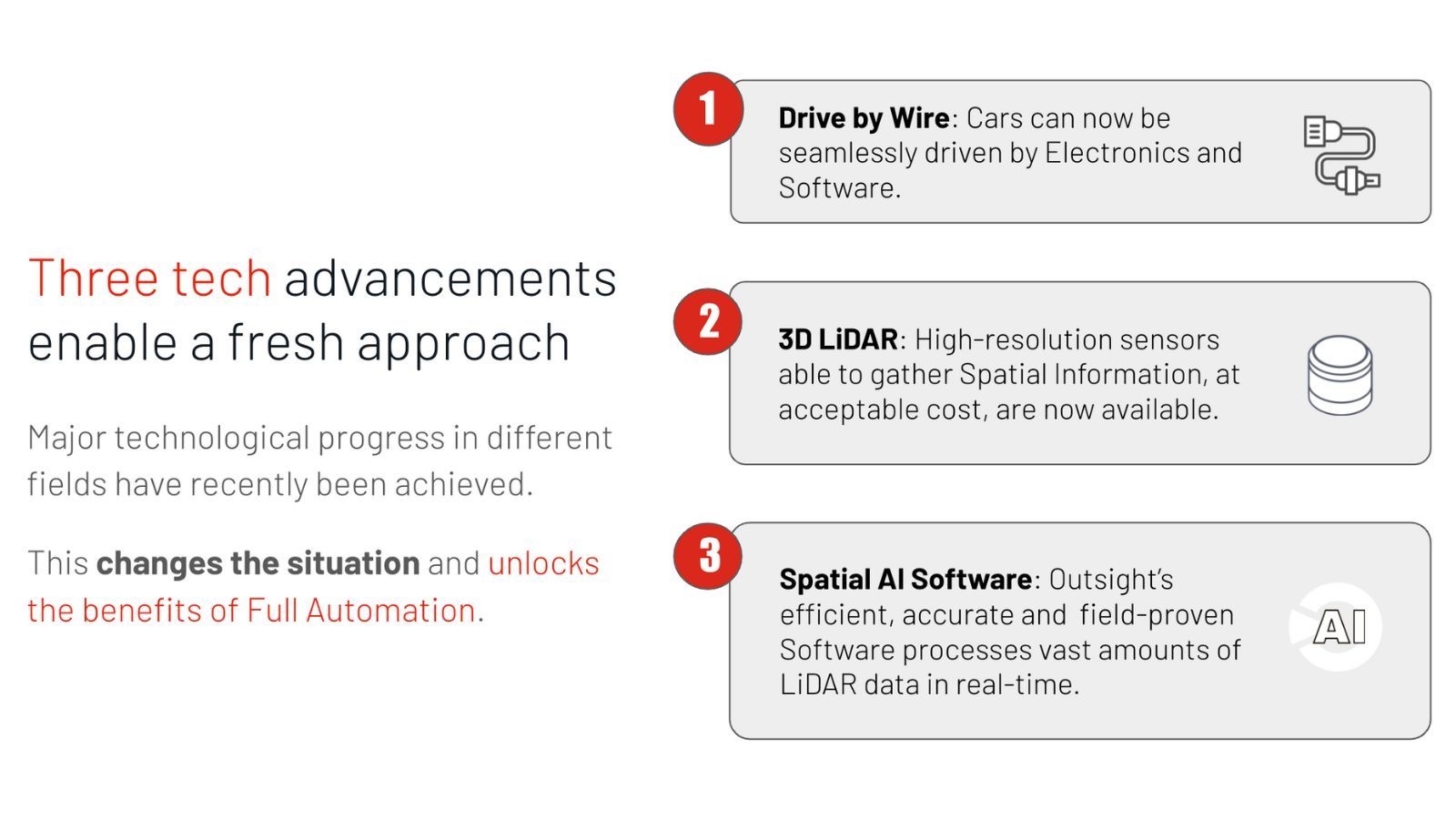
What's Roadside Automated Driving?
An automotive factory or logistics warehouse equipped with RAD (Remote Autonomous Driving) capabilities can autonomously drive designated vehicles to available parking spots without human intervention.
Unlike other types of Automated Valet Parking, where autonomous vehicles are equipped with advanced sensors such as LiDARs, these vehicles rely on infrastructure-provided situational awareness and navigation capabilities.
The system manages steering, acceleration, and braking to ensure smooth and efficient vehicle placement.
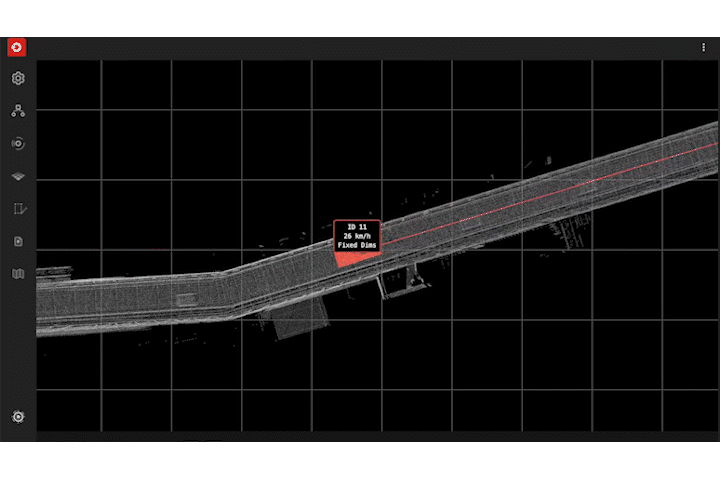
The benefits of LiDAR-powered RAD systems are multi-fold. They provide a more efficient use of space, reduce congestion, and streamline parking processes, providing a quick payback time compared to manual operations.
LiDAR's precision, when used with the right processing software, contributes to enhanced safety standards, a key consideration in these environments.
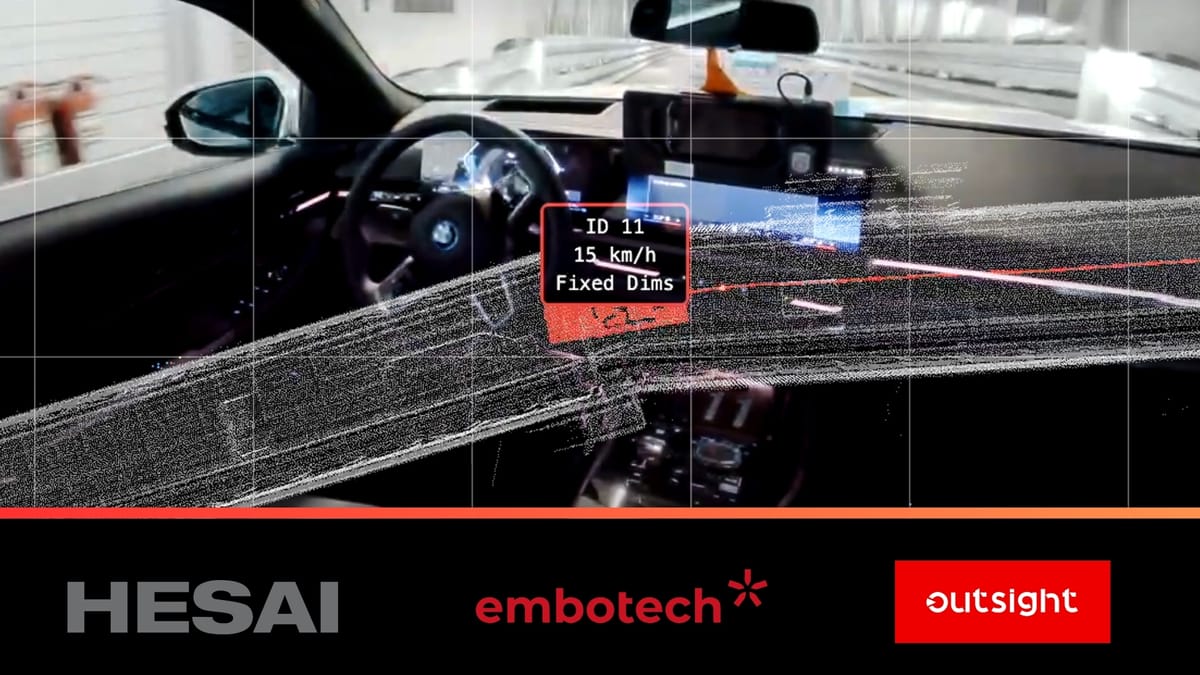
How does it work?
Fixed LIDAR sensors within the facility, thanks to the Spatial AI software, pinpoint the car's precise position and orientation as well as surrounding objects.
The information is communicated to the car in real-time, so it can drive autonomously to the parking area.
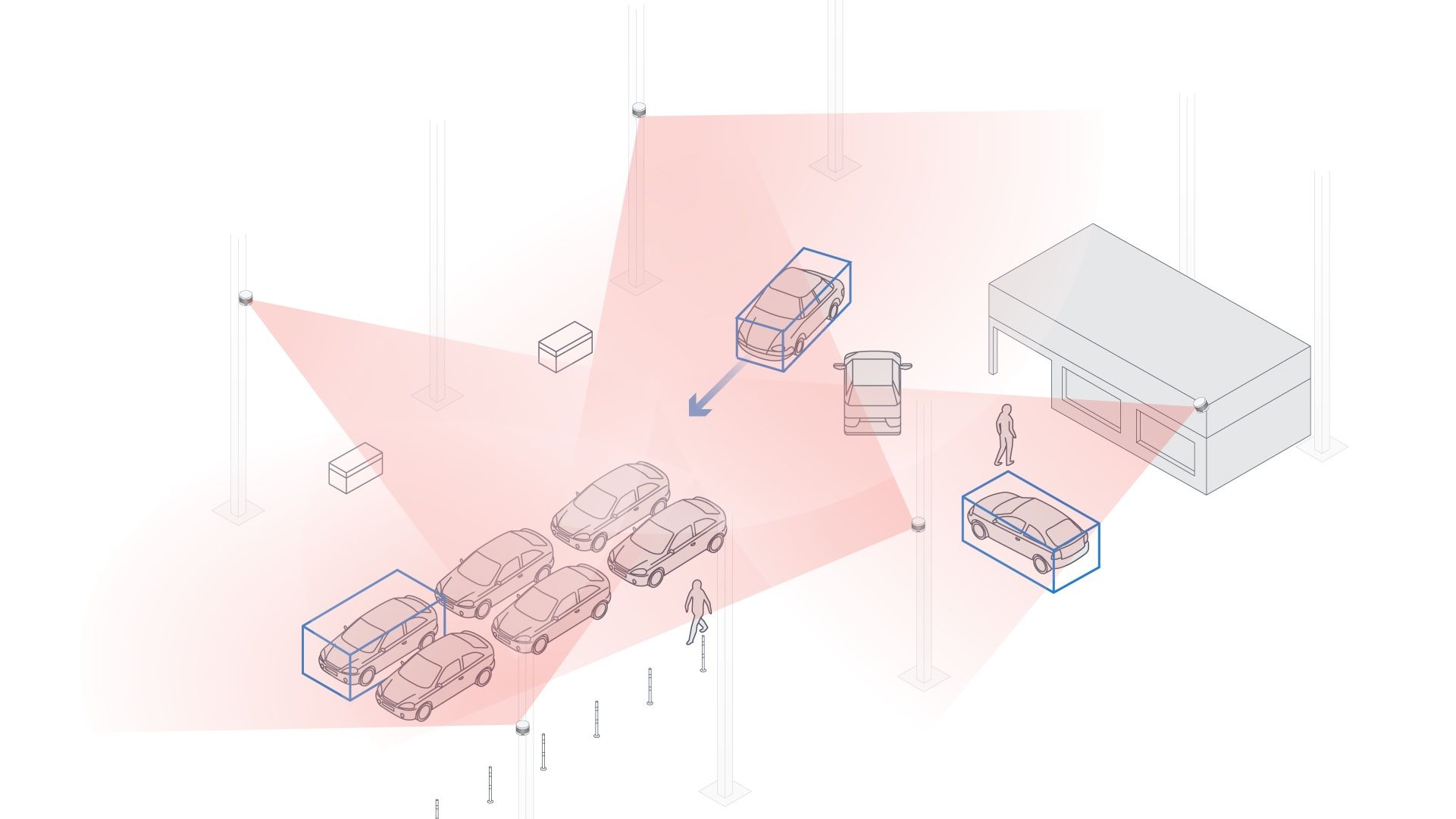

The accuracy of LiDAR is crucial for enabling accurate vehicle positioning and obstacle avoidance, ensuring the vehicles navigate safely and efficiently within the parking area.
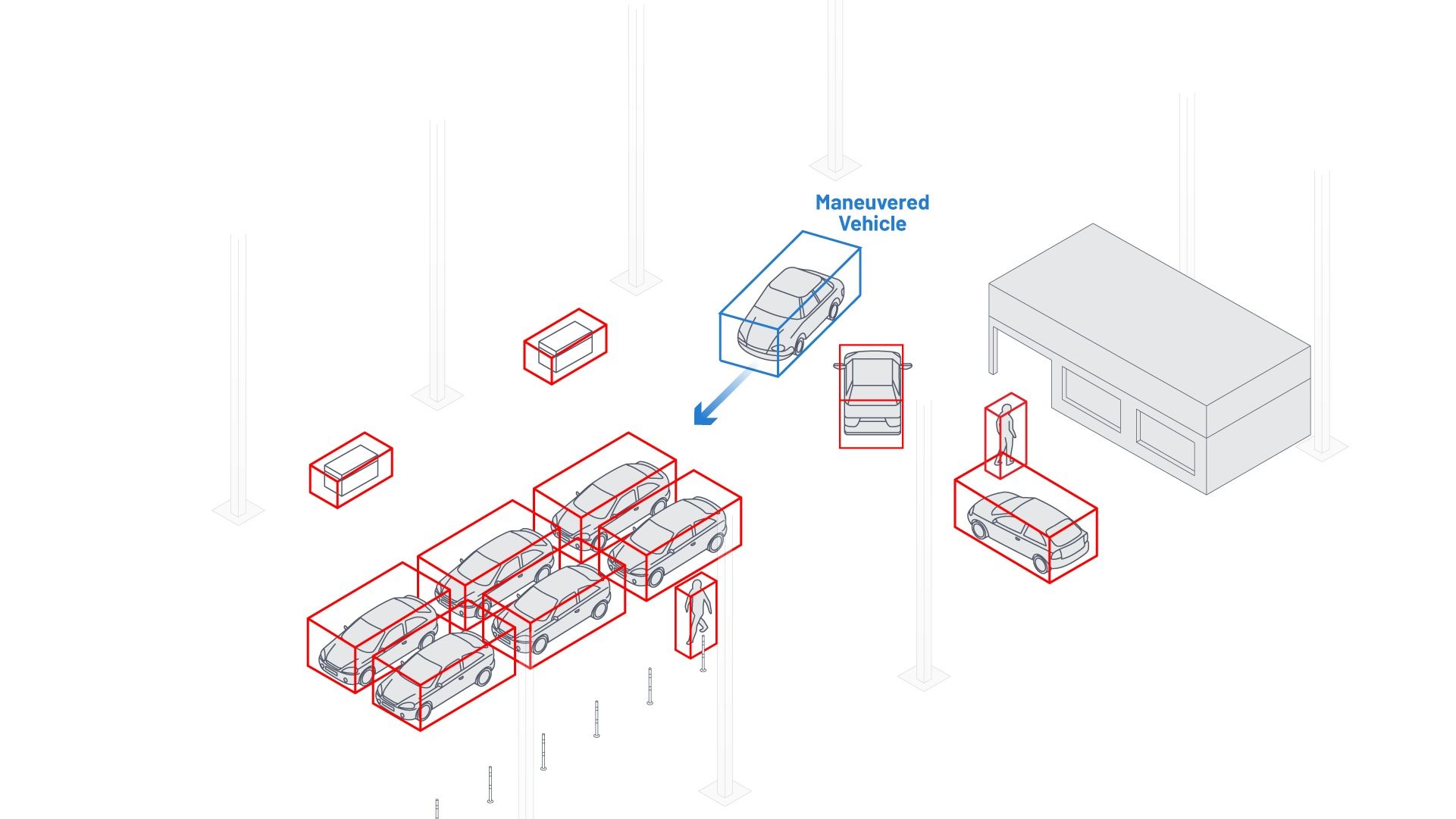
RAD also reduces the time spent handling vehicles, contributing to overall operational efficiency. The reduction of manual intervention and human error leads to a smoother, more reliable, and safer operational process.
This integration is key to the smooth operation of RAD within the broader logistical framework of an industrial setting. It facilitates real-time monitoring and control, which further enhances the system's efficiency and effectiveness.
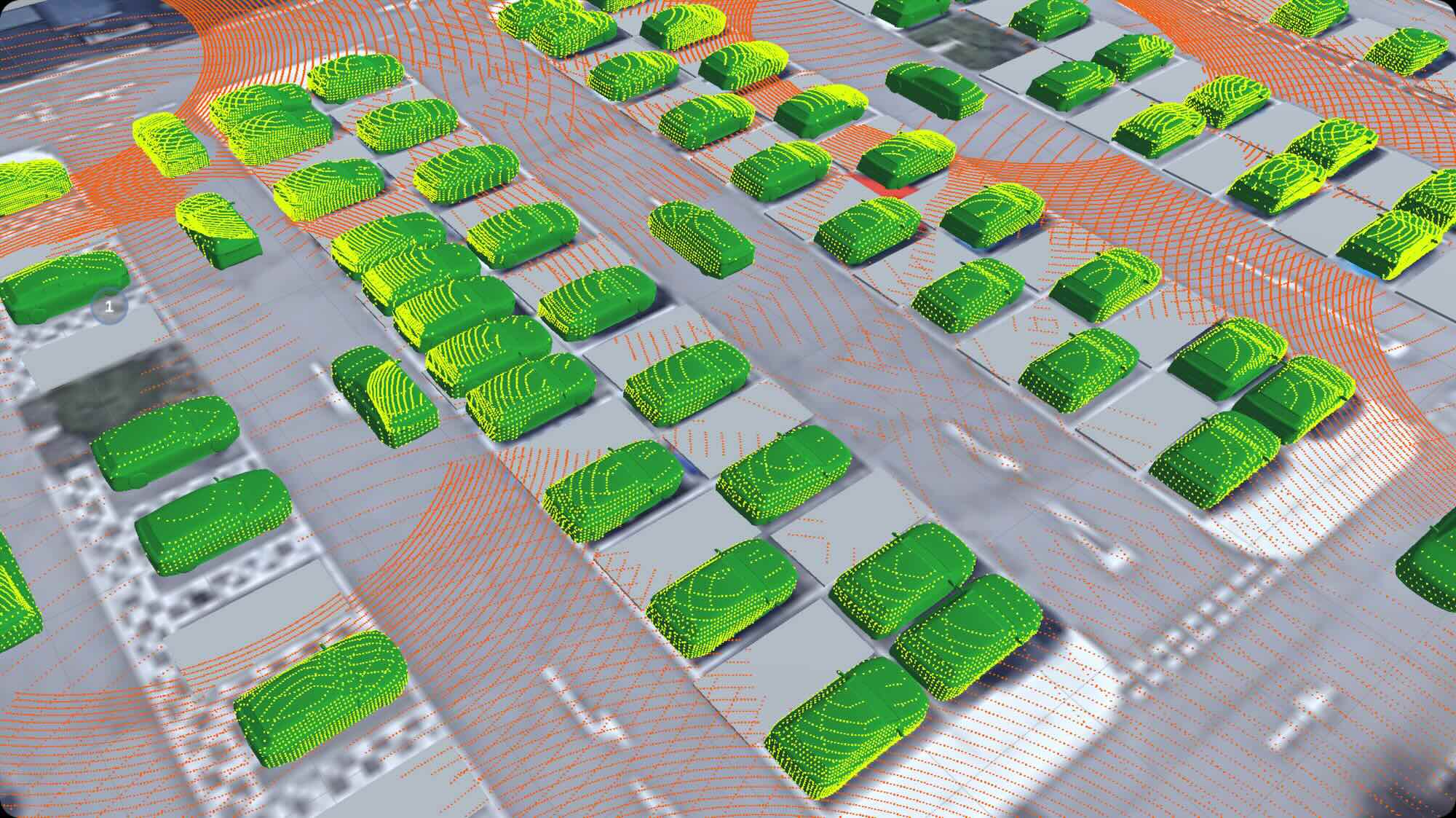
The integration of LiDAR technology in RAD systems is setting a new benchmark in automated solutions.
Of course, before automating, an automotive factory or distributor can start using LiDAR to optimise Parking operations:
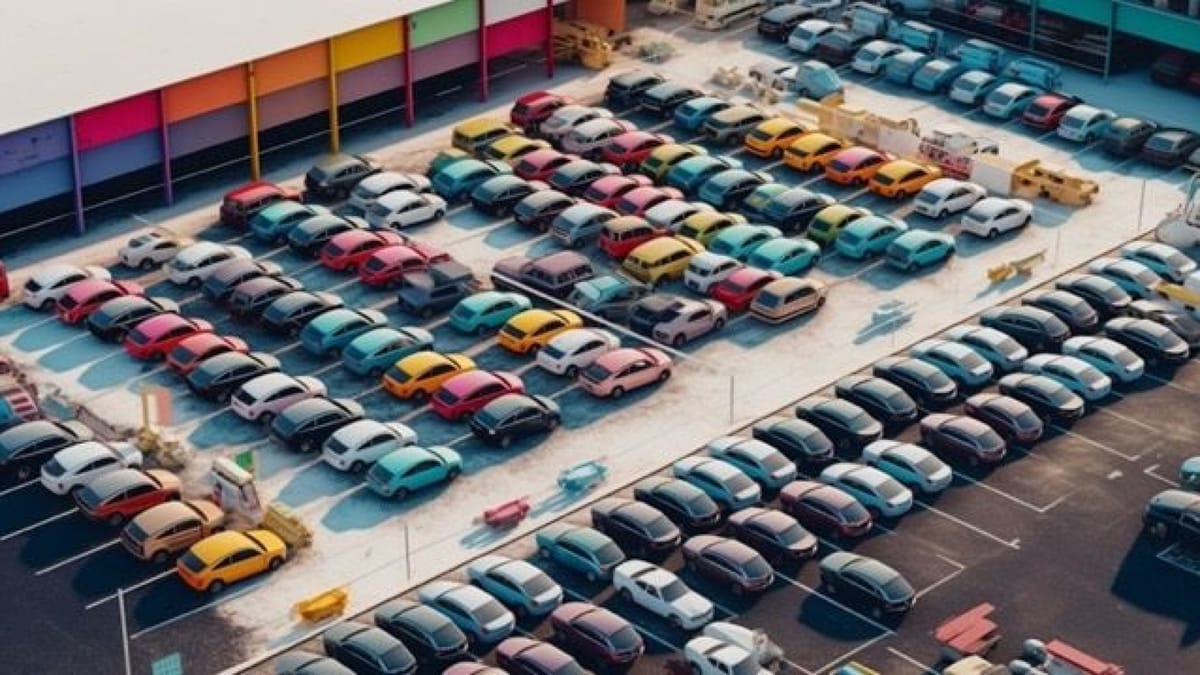
As the LiDAR market continues to grow rapidly, the potential of these technologies becomes increasingly significant.
LiDAR's precision and efficiency position it as the leading technology in this sector, promising a future where industrial parking is not just a necessity but a sophisticated, technology-driven asset integral to the operational success of industries.
In conclusion, the integration of LiDAR technology and Roadside Autonomous Driving represents a transformative shift in industrial parking, offering unparalleled accuracy, efficiency, and safety while meeting the growing demands of the AVP market.
Learn more about the power of RAD applications and how they can be implemented in real-time scenarios:
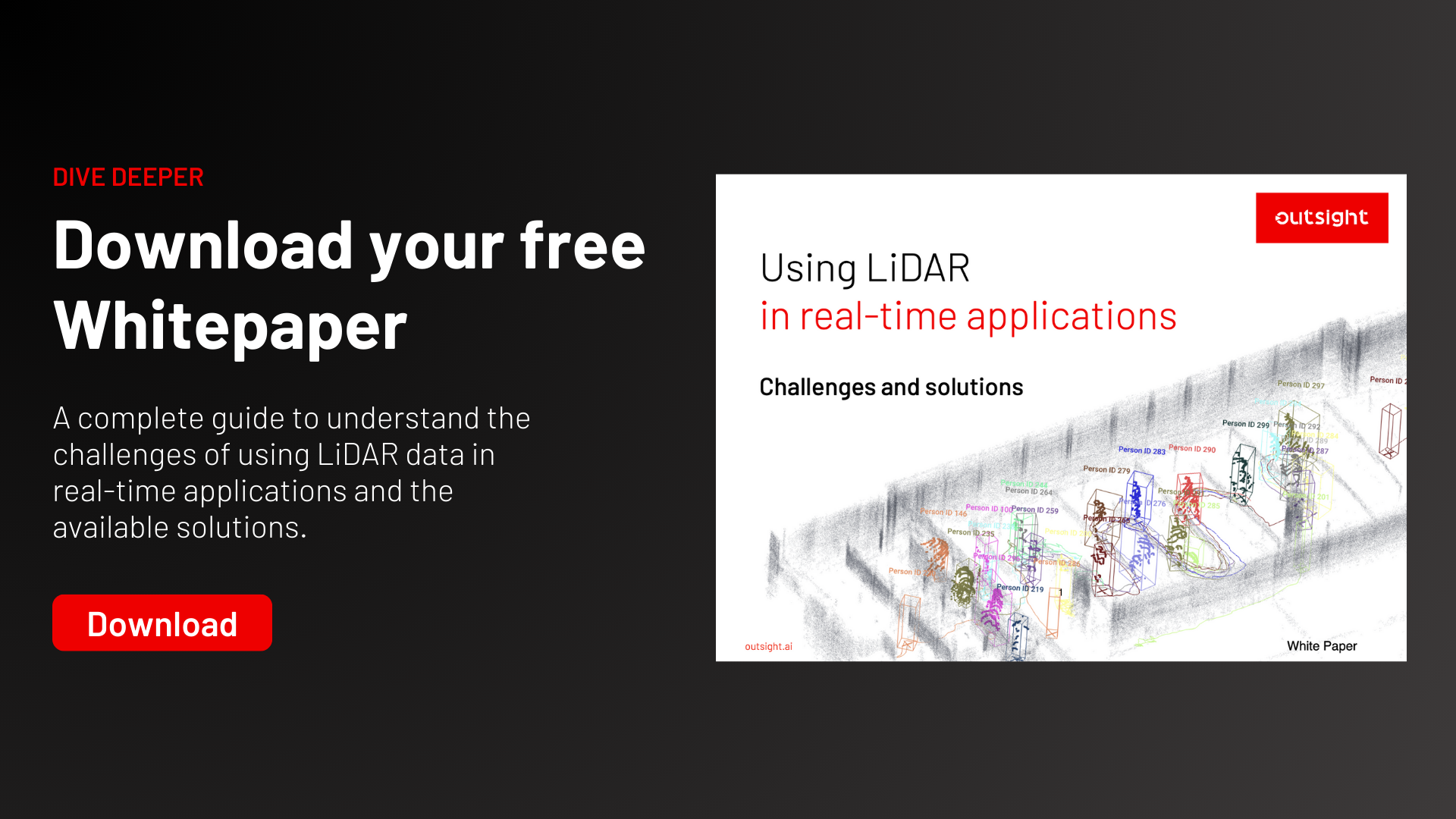